More than 50,000 people receive emergency room treatment from extension ladder-related injuries annually in the U.S. [1] and elevated falls account for roughly 88% of all fatal workplace falls [2]. It has also been found that 33% of all extension ladder accidents are caused by the base of the ladder sliding away from the supporting structure, making this the leading cause of extension ladder accidents [3]. As seen in the free body diagram of an extension ladder set up against a wall (Figure 1), the only forces counteracting the wall reaction force (FNw), which gives the ladder its propensity to slide out, are the two frictional forces, one between the foot of the ladder and ground (Ffg), and the other between the top of the ladder and the wall (Ffw). Of these two frictional forces, Ffg (the friction force at the ladder feet) is a far more significant factor in keeping the ladder from sliding backwards.
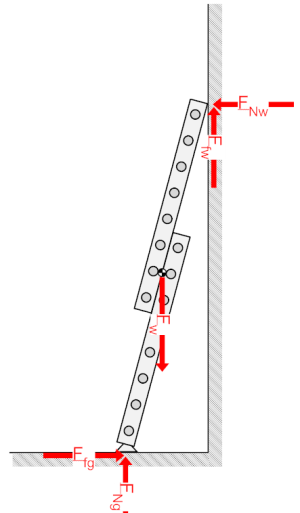
OSHA and ANSI currently attempt to maximize Ffg by warning and training users to set up their ladders at a steep incline. Following their guidelines, ladders should be set at a 4:1 rise/run ratio (roughly equating 75.5 degrees), so that for every four vertical feet the ladders extends, its base should be pushed back one foot from the wall. Despite these safety countermeasures, the average user will still set their ladder up at an angle between 57-76 degrees, with a mean set-up angle of 66.3 degrees [4]. Additionally, warnings typically indicate that ladders should be tied or held down, and that they should not be used in inclement weather, though it is not always possible or practical to follow these instructions. Since slide-outs continue to be a leading cause of extension ladder accidents, it is clear that these warning and training efforts are not having the desired effect.
When designing a product to serve a desired function, the so-called Safety Hierarchy or Hierarchy of Hazard Control should be applied to eliminate or minimize the hazards associated with that product. Generally speaking, the first priority of the product designer should be to ensure that the product can perform its intended function (in the case of extension ladders this means providing the user with the ability to access an elevated surface). Following this, the product designers must ensure that proper measures have been taken so that the product is reasonably safe while also considering whether the product is technically and economically feasible to manufacture. This safety analysis is where the application of the safety hierarchy comes into play. The safety hierarchy states that once hazards have been identified, they should be mitigated where possible in the following order of priority: 1) eliminate by design, 2) safeguard and 3) emphatically warn/train. For example, if it is impractical to change a design to eliminate a serious hazard, the next best method available is to guard against that hazard. If guarding is impractical, then instruction and/or warnings are the next best option. It should be noted that warnings are the last item on the safety hierarchy because it is generally agreed upon that they are less effective than elimination or guarding of a hazard [5]. For certain hazards that are obvious, no warnings are necessary. In the case of extension ladders, the fundamental hazard (i.e. a fall from a height) cannot be totally eliminated due to the nature of the product. However, it is possible to eliminate the specific hazard of extension ladder slide-outs by altering the design of the product. Unfortunately, ladder manufacturers have long ago abandoned attempts to eliminate this hazard by altering the design of their products and have instead opted to address this hazard almost exclusively with warnings. These warning efforts have not significantly reduced the prevalence of slide-outs, which continue to be a common cause of ladder accidents. According to the safety hierarchy, the tactic of focusing exclusively on warnings is only acceptable if product changes aimed at eliminating or mitigating the slide-out hazard have been exhausted. However, as we will show, there are still design features that could and should be installed on extension ladders that would virtually eliminate slide-out accidents.
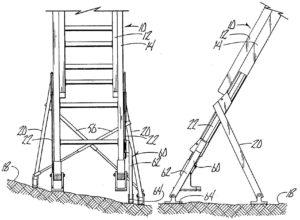
In 1988, Vernon M. Vanden Hoek was awarded U.S. patent 4,723,629 [6] titled “Extension ladder with auxiliary extension leg and supporting legs.” This patent identified the known slide-out hazard by stating that “Even if both rail lower ends engage the ground there may be slippage away from the vertical surface causing the ladder to fall and making it dangerous and unsafe.” It goes on to describe an invention for an extension ladder that consists of “independently movable leg assemblies which include legs extending at an angle to the plane of the ladder and engaging the support surface”. In short, the invention adds two smaller legs to an extension ladder near its base which, when used properly, completely prevent the possibility of the ladder base sliding back from the wall. By adding these legs near the bottom of a conventional extension ladder, Vanden Hoek’s invention provides the ladder with four points of contact to the ground in combination with the traditional two contact with the upper supporting surface. Due to the geometry of the extra legs attached at the base, the ladder will have vastly superior resistance to slide-out regardless of setup angle or surface friction. In fact, even with the traditional side rail mounted feet entirely off the ground or replaced with wheels, the ladder will still be held firmly in place!
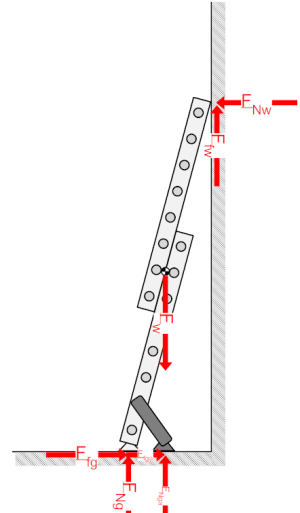
Figure 3 shows how the addition of these two legs adds another frictional force (Ffga) to counteract the weight of the ladder. Due to the geometry of these legs, if the ladder base begins to slide back away from the supporting surface, the normal force and thus the frictional force on the two auxiliary legs grows larger due to a binding effect. The result is that for the ladder to slide backward, its center of gravity must actually travel upward, which cannot happen in the absence of a large external vertical force. With this design it is virtually impossible for the ladder to slide out. Thus, this invention, if implemented as a standard feature on modern extension and straight ladders could eliminate all injuries resulting from ladder base slide-outs. While ladder manufactures have thus far chosen to ignore this safety device, there are some commercially available extension ladder accessories that work on a similar principle and demonstrate the effectiveness of such devices. [7], [8]
In summary, current extension ladder designs are a classic example of the Safety Hierarchy being disregarded by product manufacturers. Mr. Vanden Hoek’s 30 year old invention has the potential to virtually eliminate the most common cause of extension ladder accidents and yet his design has not been implemented by the major U.S. ladder manufacturers despite the fact that it is an economically and technically feasible safety feature that could prevent approximately 17,000 visits to the ER every year.
CITATIONS
[1] CPSC NEISS Database: https://www.cpsc.gov/cgibin/NEISSQuery/home.aspx
[2] Chang, C. C., W. R. Chang, and S. Matz. 2005. “The Effects of Straight Ladder Setup and Usage on Ground Reaction Forces and Friction Requirements during Ascending and Descending.” Safety Science 43.
[3] Tsipouras, S., Hendrie, J.M., Silvapulle, M.J., 2001. Ladder: accidents waiting to happen. Medical Journal of Australia 174 (10), 516–519.
[4] Young SL, Wogalter MS. On improving set-up angle accuracy for extension ladders; Paper presented at the IEA 2000/HFES 2000 Congress; San Diego, CA. 2000.
[5] Wogalter, M.S., Godfrey, S.S., Fontenelle, G.A., Desaulniers, D.R., Rothstein, P.R., Laughery, K.R., 1987b. Effectiveness of Warnings. Hum. Factors 29 (5), 599–612.
[6] Maasdam, Leonard J. Extension Ladder with Auxiliary Extension Leg and Supporting Legs. Vernon M. Vanden Hoek, assignee. Patent 4723629. 19 Feb. 1988. http://www.google.com/patents/US4723629